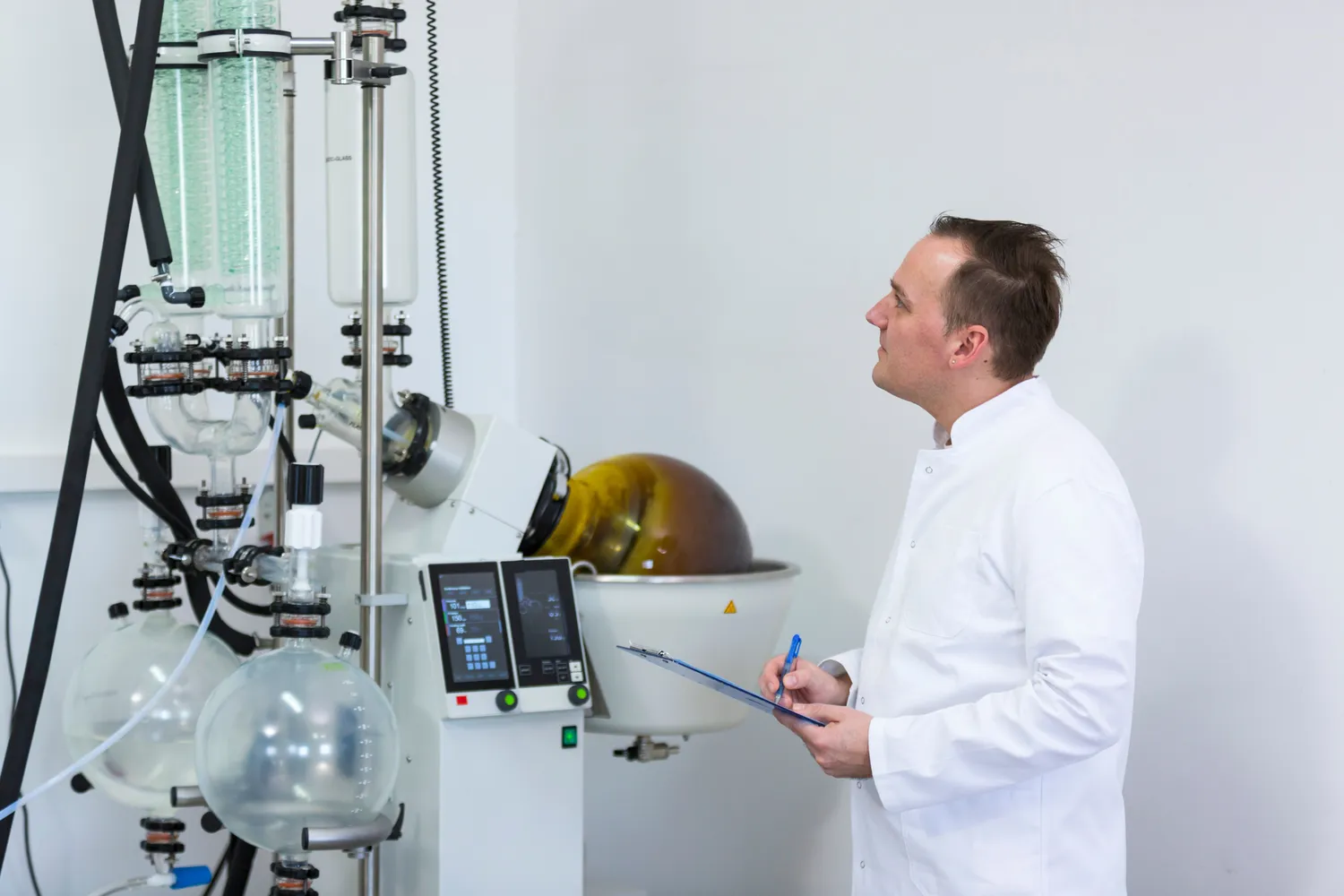
Destylarka do rozpuszczalników
Destylarka do rozpuszczalników to urządzenie, które wykorzystuje proces destylacji do oddzielania różnych substancji chemicznych na podstawie ich temperatury wrzenia. W praktyce oznacza to, że podczas podgrzewania mieszaniny rozpuszczalników, te o niższej temperaturze wrzenia parują jako pierwsze, a następnie są skraplane i zbierane w osobnym naczyniu. Proces ten jest niezwykle efektywny i pozwala na uzyskanie czystych substancji, co jest kluczowe w wielu branżach, takich jak przemysł chemiczny czy farmaceutyczny. Destylarki mogą być stosowane zarówno w małych laboratoriach, jak i w dużych zakładach produkcyjnych. Warto również zauważyć, że istnieją różne typy destylarek, w tym destylarki prostokątne oraz kolumnowe, które różnią się między sobą konstrukcją oraz zastosowaniem. Wybór odpowiedniego modelu zależy od specyfiki pracy oraz rodzaju rozpuszczalników, które mają być przetwarzane.
Jakie są zalety korzystania z destylarki do rozpuszczalników
Korzystanie z destylarki do rozpuszczalników niesie ze sobą wiele korzyści, które są istotne zarówno dla małych laboratoriów, jak i dużych zakładów przemysłowych. Po pierwsze, proces destylacji pozwala na uzyskanie wysokiej czystości substancji chemicznych, co jest kluczowe w wielu zastosowaniach. Dzięki temu można uniknąć kontaminacji produktów końcowych, co ma ogromne znaczenie w branży farmaceutycznej oraz kosmetycznej. Po drugie, destylacja jest procesem stosunkowo prostym i efektywnym, który pozwala na odzyskiwanie rozpuszczalników do dalszego użytku. To z kolei przyczynia się do zmniejszenia kosztów produkcji oraz ograniczenia odpadów chemicznych. Dodatkowo nowoczesne destylarki często wyposażone są w zaawansowane systemy monitorowania i kontroli procesów, co zwiększa ich wydajność oraz bezpieczeństwo użytkowania.
Jakie rodzaje destylarek do rozpuszczalników są dostępne na rynku
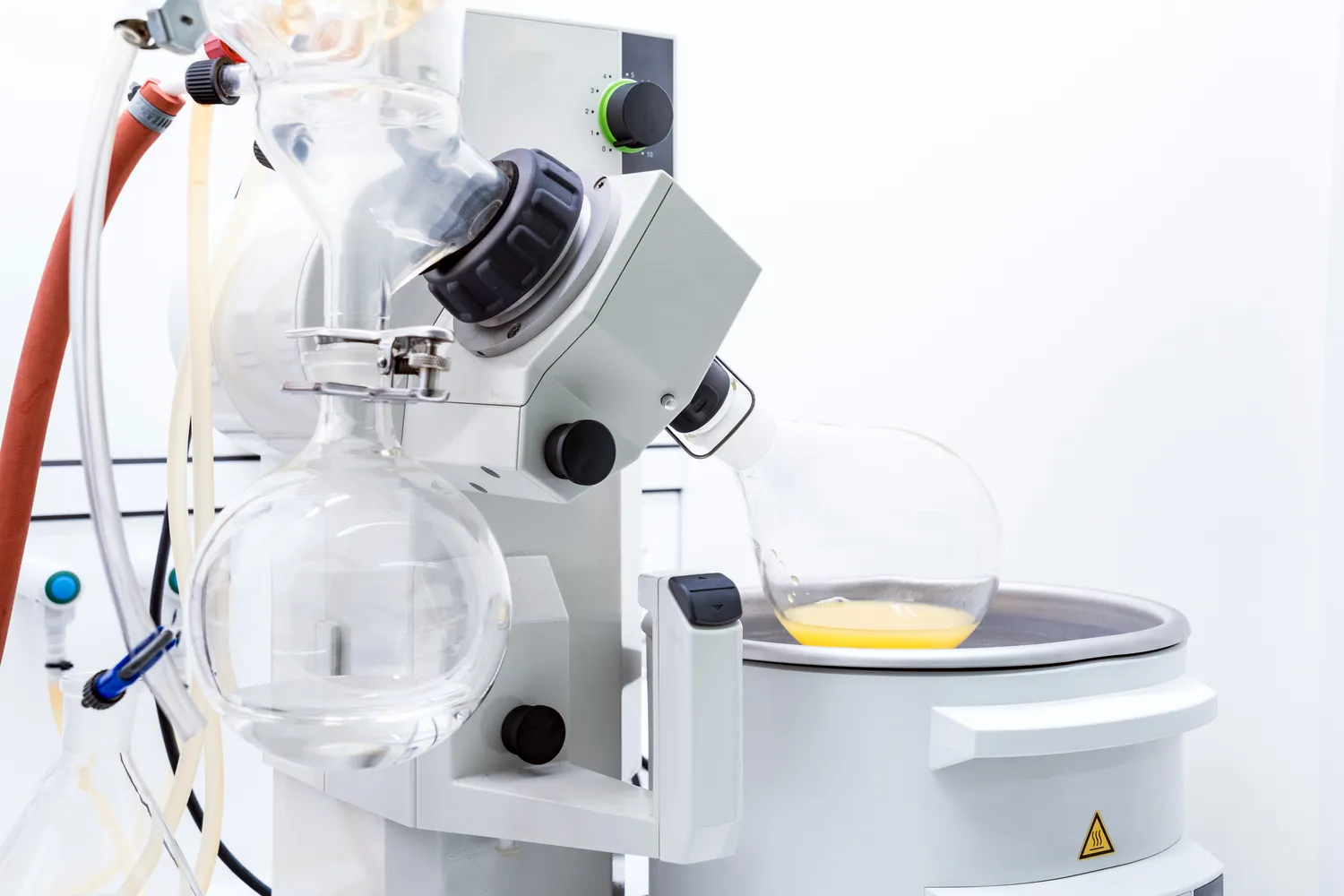
Na rynku dostępnych jest wiele różnych rodzajów destylarek do rozpuszczalników, które różnią się między sobą konstrukcją oraz przeznaczeniem. Najpopularniejsze modele to destylarki prostokątne oraz kolumnowe. Destylarki prostokątne charakteryzują się prostą budową i są często wykorzystywane w małych laboratoriach do podstawowych procesów destylacji. Z kolei destylarki kolumnowe są bardziej zaawansowane technologicznie i umożliwiają przeprowadzanie bardziej skomplikowanych procesów separacji dzięki zastosowaniu kolumny frakcyjnej. Tego typu urządzenia są idealne do przemysłowego odzyskiwania rozpuszczalników oraz oczyszczania substancji chemicznych na dużą skalę. Oprócz tego istnieją także destylarki próżniowe, które działają w obniżonym ciśnieniu i pozwalają na destylację substancji o wysokiej temperaturze wrzenia bez ryzyka ich degradacji. Wybór odpowiedniego typu destylarki powinien być uzależniony od specyfiki pracy oraz wymagań dotyczących jakości uzyskiwanych produktów.
Jakie zastosowania mają destylarki do rozpuszczalników w przemyśle
Destylarki do rozpuszczalników znajdują szerokie zastosowanie w różnych branżach przemysłowych, co czyni je niezwykle ważnym narzędziem w procesach produkcyjnych. W przemyśle chemicznym służą do oczyszczania surowców oraz odzyskiwania cennych substancji chemicznych z odpadów produkcyjnych. Dzięki temu możliwe jest zmniejszenie kosztów produkcji oraz ograniczenie negatywnego wpływu na środowisko poprzez recykling rozpuszczalników. W branży farmaceutycznej destylarki są wykorzystywane do produkcji wysokiej jakości preparatów leczniczych, gdzie czystość składników ma kluczowe znaczenie dla skuteczności terapii. Ponadto w przemyśle kosmetycznym stosuje się je do uzyskiwania czystych olejków eterycznych oraz innych składników aktywnych wykorzystywanych w kosmetykach. Również w laboratoriach badawczych destylarki odgrywają istotną rolę w analizach chemicznych oraz syntezach nowych związków organicznych.
Jakie są kluczowe elementy konstrukcyjne destylarki do rozpuszczalników
Kluczowe elementy konstrukcyjne destylarki do rozpuszczalników mają ogromny wpływ na jej wydajność oraz efektywność działania. Podstawowym elementem jest zbiornik, w którym odbywa się podgrzewanie mieszaniny rozpuszczalników. Zbiornik ten musi być wykonany z materiałów odpornych na działanie chemikaliów oraz wysokich temperatur, co zapewnia bezpieczeństwo użytkowania. Kolejnym istotnym elementem jest system grzewczy, który może być oparty na różnych źródłach energii, takich jak elektryczność, para wodna czy gaz. Wybór odpowiedniego systemu grzewczego zależy od specyfiki pracy oraz dostępnych zasobów. Ważnym komponentem jest także kolumna destylacyjna, która umożliwia separację substancji na podstawie ich temperatury wrzenia. W przypadku destylarek kolumnowych kolumna ta jest zazwyczaj wyposażona w różnego rodzaju wypełnienia lub talerze, które zwiększają powierzchnię kontaktu między parą a cieczą, co poprawia efektywność procesu destylacji. Oprócz tego nie można zapomnieć o systemie skraplania pary, który ma za zadanie schłodzenie pary i przekształcenie jej w ciecz. Skraplacz powinien być dobrze izolowany, aby zminimalizować straty ciepła oraz zapewnić optymalne warunki pracy.
Jakie czynniki wpływają na wybór destylarki do rozpuszczalników
Wybór odpowiedniej destylarki do rozpuszczalników jest kluczowy dla efektywności procesów produkcyjnych oraz jakości uzyskiwanych produktów. Istnieje wiele czynników, które należy wziąć pod uwagę przy podejmowaniu decyzji o zakupie tego typu urządzenia. Po pierwsze, należy określić rodzaj rozpuszczalników, które będą przetwarzane. Różne substancje chemiczne mają różne temperatury wrzenia oraz właściwości fizykochemiczne, co może wpłynąć na wybór konkretnego modelu destylarki. Po drugie, istotne jest określenie wydajności urządzenia, czyli ilości substancji, które można przetworzyć w określonym czasie. Wydajność ta powinna być dostosowana do potrzeb produkcyjnych danego zakładu. Kolejnym czynnikiem jest dostępność miejsca na instalację destylarki oraz infrastruktura techniczna zakładu, która musi być przystosowana do obsługi tego typu urządzeń. Należy również zwrócić uwagę na koszty eksploatacji oraz konserwacji destylarki, ponieważ mogą one znacząco wpłynąć na rentowność całego procesu produkcyjnego.
Jakie są najczęstsze błędy przy używaniu destylarki do rozpuszczalników
Użytkowanie destylarki do rozpuszczalników wiąże się z pewnymi ryzykami i wymaga przestrzegania określonych zasad bezpieczeństwa oraz procedur operacyjnych. Niestety, wiele osób popełnia błędy, które mogą prowadzić do niebezpiecznych sytuacji lub obniżenia efektywności procesu destylacji. Jednym z najczęstszych błędów jest niewłaściwe przygotowanie materiałów przed rozpoczęciem procesu. Niezgodność składników chemicznych lub ich zanieczyszczenie może prowadzić do nieefektywnej separacji substancji oraz obniżenia jakości uzyskiwanych produktów. Innym powszechnym błędem jest niewłaściwe ustawienie parametrów pracy destylarki, takich jak temperatura czy ciśnienie. Zbyt wysoka temperatura może prowadzić do degradacji substancji chemicznych, natomiast zbyt niskie ciśnienie może skutkować niepełnym procesem destylacji. Ważne jest również regularne monitorowanie stanu technicznego urządzenia oraz przeprowadzanie konserwacji zgodnie z zaleceniami producenta. Zaniedbanie tych kwestii może prowadzić do awarii sprzętu i kosztownych przestojów w produkcji.
Jakie są nowoczesne technologie w dziedzinie destylacji rozpuszczalników
Nowoczesne technologie w dziedzinie destylacji rozpuszczalników rozwijają się dynamicznie i mają na celu zwiększenie efektywności procesów separacyjnych oraz poprawę bezpieczeństwa użytkowania urządzeń. Jednym z najnowszych trendów jest zastosowanie technologii membranowych, które pozwalają na separację substancji chemicznych bez konieczności podgrzewania ich do wysokich temperatur. Dzięki temu możliwe jest ograniczenie zużycia energii oraz minimalizacja ryzyka degradacji cennych składników. Innowacyjne rozwiązania obejmują także automatyzację procesów destylacyjnych poprzez zastosowanie zaawansowanych systemów sterowania i monitorowania, które pozwalają na precyzyjne dostosowywanie parametrów pracy urządzenia w czasie rzeczywistym. Dodatkowo nowoczesne destylarki często wyposażone są w technologie odzysku ciepła, co pozwala na zwiększenie efektywności energetycznej całego procesu. Warto również zwrócić uwagę na rozwój materiałów konstrukcyjnych wykorzystywanych w budowie destylarek, które charakteryzują się większą odpornością na działanie agresywnych substancji chemicznych oraz wysokich temperatur.
Jakie są przepisy prawne dotyczące użytkowania destylarek do rozpuszczalników
Użytkowanie destylarek do rozpuszczalników wiąże się z koniecznością przestrzegania szeregu przepisów prawnych dotyczących ochrony zdrowia i środowiska. W wielu krajach istnieją szczegółowe regulacje dotyczące pracy z substancjami chemicznymi, które mają na celu zapewnienie bezpieczeństwa zarówno pracowników, jak i otoczenia. Przepisy te obejmują m.in. wymagania dotyczące oznakowania substancji chemicznych, przechowywania ich w odpowiednich warunkach oraz stosowania środków ochrony osobistej przez pracowników obsługujących urządzenia takie jak destylarki. Ponadto przedsiębiorstwa muszą przestrzegać norm dotyczących emisji substancji szkodliwych do atmosfery oraz zarządzania odpadami chemicznymi powstającymi w wyniku procesów produkcyjnych. Warto również pamiętać o konieczności przeprowadzania regularnych audytów i inspekcji dotyczących przestrzegania przepisów BHP oraz ochrony środowiska przez odpowiednie organy kontrolne.
Jak dbać o bezpieczeństwo podczas pracy z destylarką do rozpuszczalników
Dbanie o bezpieczeństwo podczas pracy z destylarką do rozpuszczalników jest kluczowe dla ochrony zdrowia pracowników oraz minimalizacji ryzyka wystąpienia niebezpiecznych sytuacji związanych z obsługą substancji chemicznych. Przede wszystkim należy przestrzegać zasad BHP i stosować odpowiednie środki ochrony osobistej, takie jak rękawice ochronne, gogle czy maski filtrujące, aby zabezpieczyć się przed kontaktem z niebezpiecznymi oparami lub cieczy. Ważne jest również zapewnienie odpowiedniej wentylacji w pomieszczeniu, w którym znajduje się destylarka, aby uniknąć gromadzenia się szkodliwych gazów i oparów chemicznych. Przed rozpoczęciem pracy warto dokładnie zapoznać się z instrukcją obsługi urządzenia oraz przeprowadzić szkolenie dla wszystkich pracowników zaangażowanych w proces produkcji.