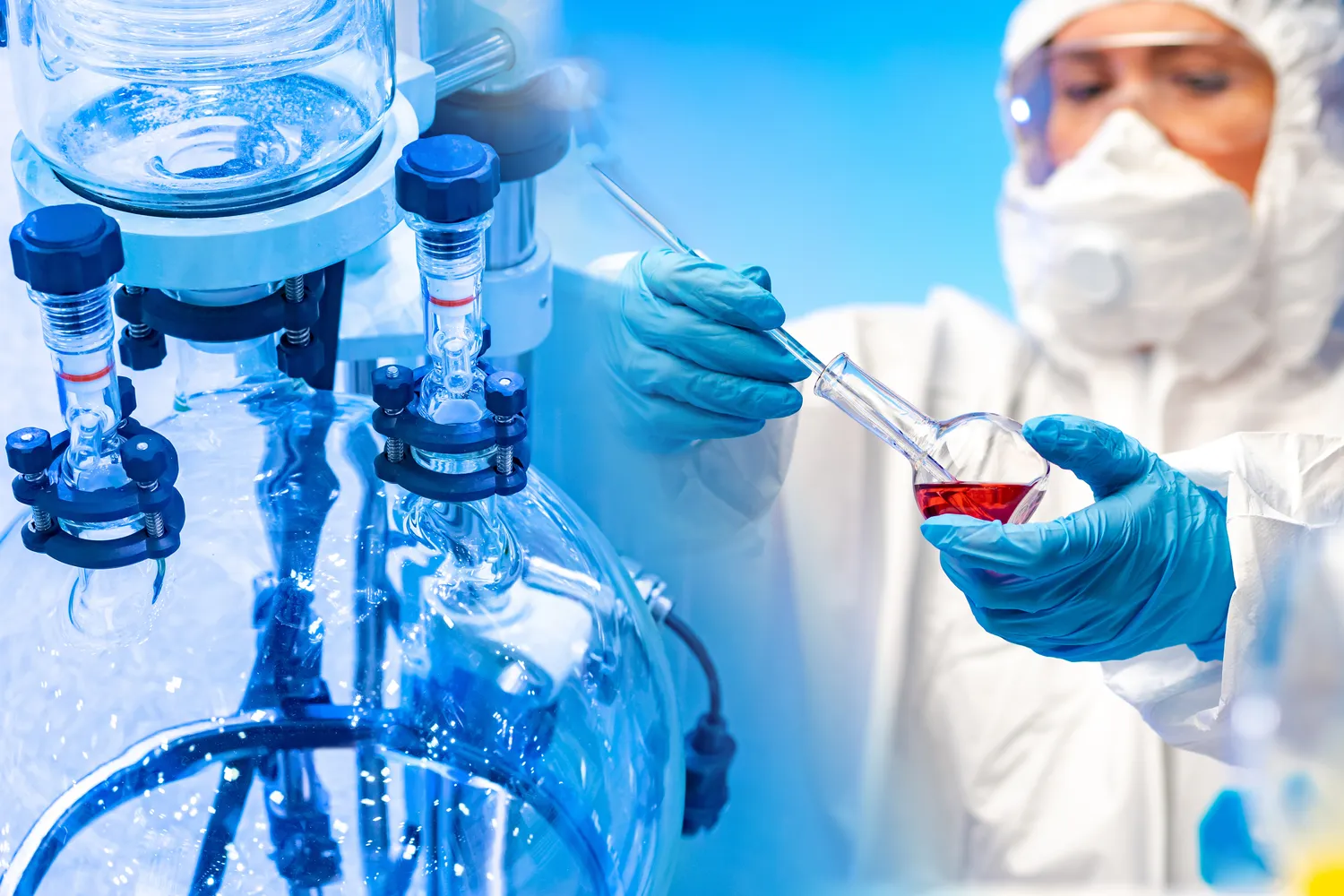
Destylarka do rozpuszczalnika
Destylarka do rozpuszczalnika to urządzenie, które wykorzystuje proces destylacji do oddzielania różnych substancji chemicznych na podstawie ich temperatury wrzenia. W praktyce oznacza to, że gdy mieszanina rozpuszczalników jest podgrzewana, substancje o niższej temperaturze wrzenia parują jako pierwsze, a następnie są skraplane i zbierane w osobnym naczyniu. Proces ten jest niezwykle efektywny i pozwala na uzyskanie czystych substancji chemicznych, które mogą być używane w różnych zastosowaniach przemysłowych i laboratoryjnych. W przypadku destylarek do rozpuszczalników kluczowe jest również odpowiednie zarządzanie temperaturą oraz ciśnieniem, co wpływa na wydajność całego procesu. Warto również zwrócić uwagę na konstrukcję destylarki, która powinna być wykonana z materiałów odpornych na działanie chemikaliów, aby zapewnić bezpieczeństwo użytkowania oraz długowieczność urządzenia.
Jakie są główne zastosowania destylarki do rozpuszczalnika
Destylarka do rozpuszczalnika ma wiele zastosowań w różnych dziedzinach przemysłu oraz nauki. Przede wszystkim jest wykorzystywana w laboratoriach chemicznych do oczyszczania substancji oraz separacji składników mieszanin. Dzięki temu możliwe jest uzyskanie wysokiej czystości reagentów, co jest kluczowe w wielu eksperymentach oraz procesach badawczych. W przemyśle farmaceutycznym destylarki służą do produkcji czystych substancji czynnych, które są niezbędne w produkcji leków. Ponadto w branży kosmetycznej destylacja pozwala na uzyskanie esencji zapachowych oraz innych składników aktywnych, które są stosowane w kosmetykach. W przemyśle petrochemicznym destylarki są wykorzystywane do separacji różnych frakcji ropy naftowej, co umożliwia produkcję paliw oraz innych produktów chemicznych. Również w przemyśle spożywczym destylacja znajduje zastosowanie przy produkcji alkoholi oraz ekstraktów smakowych.
Jakie rodzaje destylarek do rozpuszczalnika można znaleźć
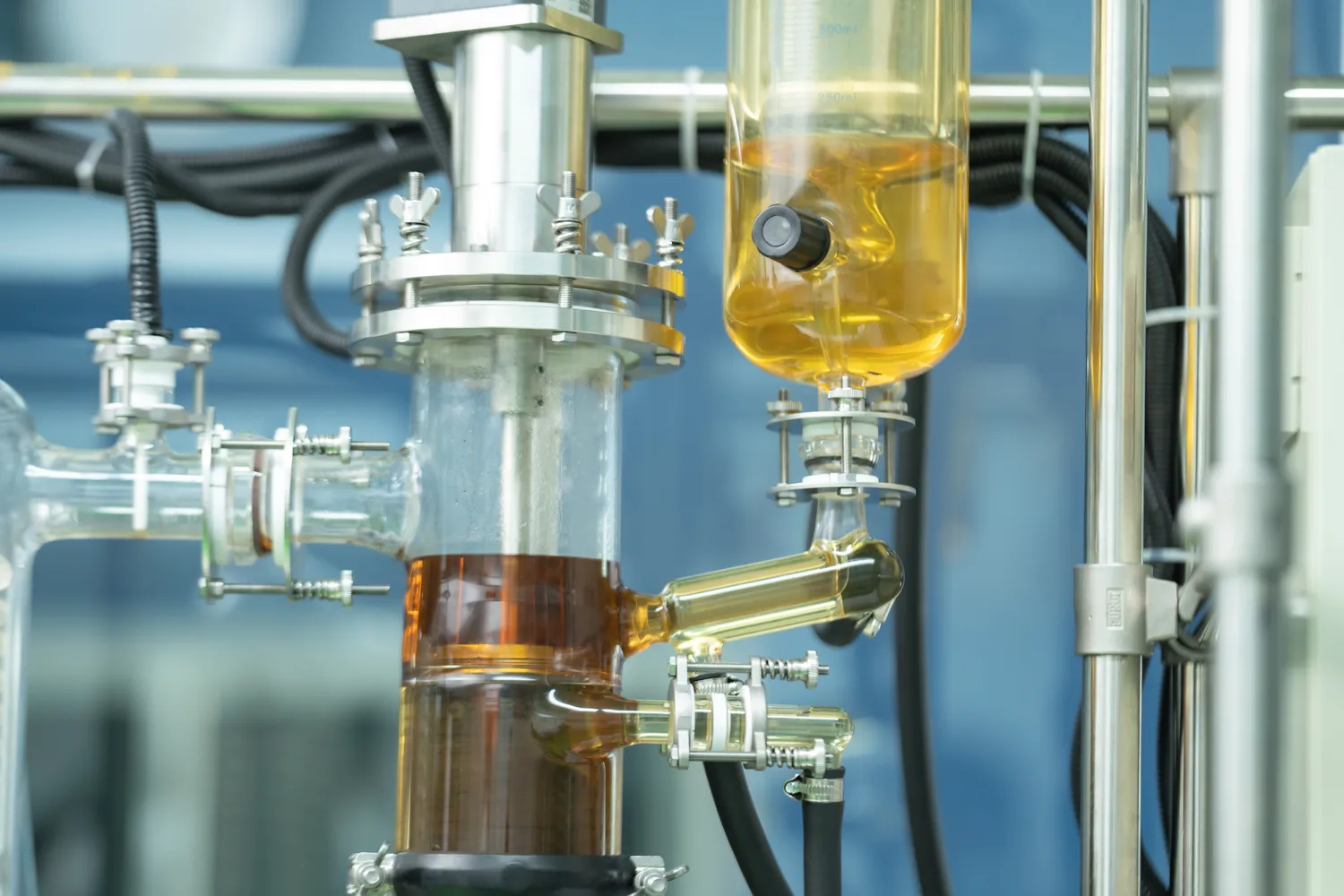
Na rynku dostępnych jest wiele rodzajów destylarek do rozpuszczalników, które różnią się zarówno konstrukcją, jak i przeznaczeniem. Jednym z najpopularniejszych typów są destylarki prostokątne, które charakteryzują się dużą pojemnością i wydajnością. Są one idealne dla dużych zakładów przemysłowych oraz laboratoriów, gdzie wymagana jest szybka separacja dużych ilości substancji. Innym rodzajem są destylarki kolumnowe, które umożliwiają bardziej zaawansowaną separację dzięki zastosowaniu kolumny frakcyjnej. Tego typu urządzenia są szczególnie przydatne w przemyśle petrochemicznym oraz farmaceutycznym, gdzie wymagana jest wysoka jakość uzyskiwanych produktów. Dla mniejszych laboratoriów i zastosowań domowych dostępne są także kompaktowe destylarki, które zajmują mniej miejsca i są łatwiejsze w obsłudze. Te urządzenia często mają ograniczoną pojemność, ale doskonale sprawdzają się w mniejszych projektach badawczych czy hobbystycznych.
Jakie materiały są najlepsze do budowy destylarki
Budowa destylarki do rozpuszczalnika wymaga zastosowania odpowiednich materiałów, które będą odporne na działanie chemikaliów oraz wysokich temperatur. Najczęściej wykorzystywanym materiałem jest stal nierdzewna, która charakteryzuje się wysoką odpornością na korozję i łatwością w utrzymaniu czystości. Stal nierdzewna zapewnia również trwałość konstrukcji, co jest istotne w kontekście długotrwałego użytkowania urządzenia. Inne materiały stosowane w budowie destylarek to szkło borokrzemowe oraz teflon, które również wykazują wysoką odporność na działanie agresywnych substancji chemicznych. Szkło borokrzemowe jest często wykorzystywane w elementach takich jak kolby czy chłodnice ze względu na swoje właściwości termiczne i chemiczne. Teflon natomiast znajduje zastosowanie w uszczelkach oraz elementach kontaktujących się z agresywnymi substancjami ze względu na swoją niską adhezję i odporność na wysokie temperatury.
Jakie czynniki wpływają na efektywność destylacji w destylarce
Efektywność procesu destylacji w destylarce do rozpuszczalnika zależy od wielu czynników, które mogą znacząco wpłynąć na jakość uzyskiwanego produktu oraz wydajność całego procesu. Kluczowym elementem jest temperatura, która musi być precyzyjnie kontrolowana, aby zapewnić optymalne warunki dla parowania i skraplania substancji. Zbyt wysoka temperatura może prowadzić do niepożądanych reakcji chemicznych, podczas gdy zbyt niska może skutkować niedostatecznym oddzieleniem składników. Innym ważnym czynnikiem jest ciśnienie, które również wpływa na temperatury wrzenia substancji. W przypadku destylacji pod próżnią możliwe jest obniżenie temperatury wrzenia, co jest szczególnie przydatne w przypadku substancji wrażliwych na wysoką temperaturę. Dodatkowo, konstrukcja samej destylarki ma znaczenie – odpowiednio zaprojektowane kolumny frakcyjne czy chłodnice mogą zwiększyć efektywność separacji. Warto również zwrócić uwagę na jakość używanych materiałów oraz ich czystość, ponieważ zanieczyszczenia mogą wpłynąć na wyniki destylacji.
Jakie są najczęstsze problemy z destylarkami do rozpuszczalnika
Podczas użytkowania destylarek do rozpuszczalników mogą wystąpić różnorodne problemy, które mogą wpłynąć na efektywność procesu oraz jakość uzyskiwanych produktów. Jednym z najczęstszych problemów jest zatykanie się kolumny frakcyjnej lub innych elementów urządzenia, co może prowadzić do obniżenia wydajności destylacji. Zatykanie się może być spowodowane osadzaniem się zanieczyszczeń lub nieodpowiednim doborem materiałów. Innym problemem może być niewłaściwe zarządzanie temperaturą i ciśnieniem, co prowadzi do nieefektywnej separacji składników. Zbyt wysoka temperatura może powodować degradację substancji, a zbyt niska może skutkować ich niepełnym oddzieleniem. Dodatkowo, niewłaściwe uszczelnienie połączeń może prowadzić do wycieków pary lub cieczy, co jest nie tylko niebezpieczne, ale także wpływa na jakość uzyskiwanego produktu. Warto również zwrócić uwagę na regularne przeglądy i konserwację urządzenia, aby uniknąć problemów związanych z zużyciem materiałów czy uszkodzeniami mechanicznymi.
Jakie są koszty zakupu i eksploatacji destylarki do rozpuszczalnika
Koszty zakupu oraz eksploatacji destylarki do rozpuszczalnika mogą się znacznie różnić w zależności od wielu czynników, takich jak typ urządzenia, jego pojemność oraz zastosowane technologie. Na rynku dostępne są zarówno proste modele przeznaczone dla hobbystów, jak i zaawansowane urządzenia przemysłowe o dużej wydajności. Ceny prostych destylarek zaczynają się od kilkuset złotych, natomiast bardziej zaawansowane modele mogą kosztować nawet kilka tysięcy złotych lub więcej. Oprócz kosztu zakupu warto uwzględnić także wydatki związane z eksploatacją urządzenia. Należą do nich koszty energii elektrycznej potrzebnej do podgrzewania substancji oraz koszty materiałów eksploatacyjnych, takich jak uszczelki czy elementy filtrujące. Dodatkowo należy pamiętać o regularnych przeglądach technicznych oraz ewentualnych naprawach, które mogą generować dodatkowe koszty.
Jakie są różnice między destylarkami a innymi metodami separacji
Destylacja to jedna z wielu metod separacji substancji chemicznych, a jej wybór zależy od specyfiki danego procesu oraz właściwości separowanych składników. W porównaniu do innych metod, takich jak ekstrakcja czy filtracja, destylacja charakteryzuje się większą precyzją w oddzielaniu składników na podstawie ich temperatury wrzenia. Ekstrakcja polega na wykorzystaniu rozpuszczalników do wydobywania określonych substancji z mieszanin, co może być mniej efektywne w przypadku substancji o podobnych właściwościach chemicznych. Filtracja natomiast jest procesem mechanicznym polegającym na oddzielaniu ciał stałych od cieczy i nie sprawdza się w przypadku mieszanin ciekłych zawierających różne substancje chemiczne. Destylacja pozwala na uzyskanie wyższej czystości produktów końcowych oraz lepszą kontrolę nad procesem separacji. Ponadto destylarka do rozpuszczalnika umożliwia ciągłą pracę i automatyzację procesu, co zwiększa wydajność produkcji w porównaniu do tradycyjnych metod separacji.
Jakie są nowoczesne technologie w budowie destylarek
Nowoczesne technologie stosowane w budowie destylarek do rozpuszczalników znacząco poprawiają ich wydajność oraz efektywność działania. Wiele współczesnych urządzeń wykorzystuje systemy automatyzacji i monitorowania procesów, co pozwala na precyzyjne zarządzanie parametrami pracy oraz minimalizację ryzyka błędów ludzkich. Dzięki zastosowaniu zaawansowanych czujników możliwe jest bieżące śledzenie temperatury i ciśnienia wewnątrz destylarki, co umożliwia szybką reakcję w przypadku wykrycia nieprawidłowości. Ponadto nowoczesne materiały konstrukcyjne, takie jak kompozyty czy nanomateriały, zwiększają odporność urządzeń na działanie agresywnych substancji chemicznych oraz wysokich temperatur. Innowacyjne rozwiązania inżynieryjne pozwalają także na zmniejszenie zużycia energii poprzez zastosowanie bardziej efektywnych systemów grzewczych oraz izolacyjnych. Warto również zwrócić uwagę na rozwój technologii odzysku ciepła odpadowego, które pozwala na ponowne wykorzystanie energii generowanej podczas procesu destylacji.
Jakie są przepisy dotyczące użytkowania destylarek
Użytkowanie destylarek do rozpuszczalników wiąże się z przestrzeganiem szeregu przepisów prawnych oraz norm bezpieczeństwa mających na celu ochronę zdrowia ludzi i środowiska naturalnego. Przepisy te różnią się w zależności od kraju oraz regionu i obejmują zarówno regulacje dotyczące produkcji chemikaliów, jak i zasady dotyczące bezpieczeństwa pracy w laboratoriach czy zakładach przemysłowych. W wielu krajach konieczne jest uzyskanie odpowiednich zezwoleń przed rozpoczęciem działalności związanej z używaniem destylarek, szczególnie jeśli dotyczy to substancji chemicznych o wysokim ryzyku dla zdrowia lub środowiska. Pracownicy obsługujący destylarki muszą być odpowiednio przeszkoleni w zakresie bezpieczeństwa pracy oraz znajomości procedur awaryjnych związanych z użytkowaniem tych urządzeń. Dodatkowo istotne jest przestrzeganie zasad dotyczących przechowywania substancji chemicznych oraz utylizacji odpadów powstałych podczas procesu destylacji.