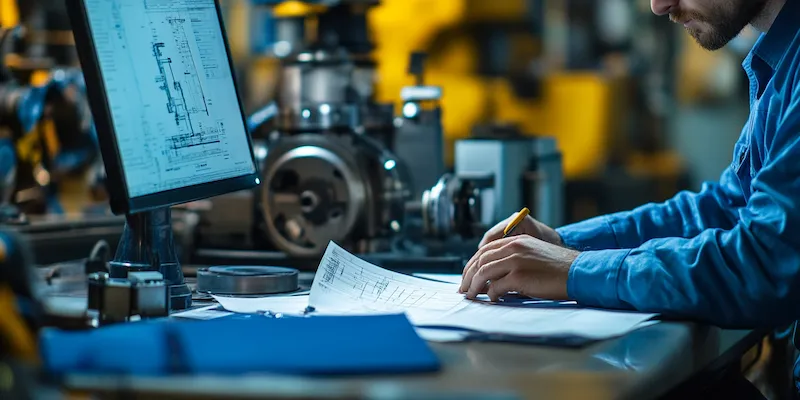
Budowa maszyn pneumatycznych
Budowa maszyn pneumatycznych opiera się na kilku kluczowych elementach, które współpracują ze sobą w celu zapewnienia efektywnego działania systemu. Podstawowym komponentem jest sprężarka, która odpowiada za wytwarzanie sprężonego powietrza. Sprężone powietrze jest następnie kierowane do zbiornika, gdzie gromadzone jest w celu późniejszego wykorzystania. Kolejnym istotnym elementem jest układ rozdzielaczy, który kontroluje przepływ powietrza do poszczególnych części maszyny. W systemie pneumatycznym znajdują się również siłowniki, które przekształcają energię sprężonego powietrza w ruch mechaniczny. Dodatkowo, w budowie maszyn pneumatycznych uwzględnia się różnego rodzaju zawory, które regulują ciśnienie i przepływ powietrza, a także filtry, które oczyszczają powietrze z zanieczyszczeń. Warto również wspomnieć o wężach i rurkach, które transportują sprężone powietrze pomiędzy poszczególnymi elementami maszyny.
Jakie są zalety i wady maszyn pneumatycznych
Maszyny pneumatyczne mają wiele zalet, które czynią je atrakcyjnym rozwiązaniem w różnych branżach przemysłowych. Przede wszystkim charakteryzują się dużą niezawodnością oraz prostotą konstrukcji, co ułatwia ich konserwację i naprawy. Dzięki zastosowaniu sprężonego powietrza jako medium roboczego, maszyny te są bezpieczne dla użytkowników i środowiska. Ponadto, systemy pneumatyczne mogą działać w ekstremalnych warunkach temperaturowych oraz są odporne na działanie substancji chemicznych. Warto jednak zauważyć, że maszyny pneumatyczne mają również swoje ograniczenia. Jednym z głównych minusów jest konieczność posiadania sprężarki oraz zbiornika na sprężone powietrze, co wiąże się z dodatkowymi kosztami inwestycyjnymi oraz przestrzenią potrzebną do ich zainstalowania. Dodatkowo, efektywność energetyczna systemów pneumatycznych może być niższa w porównaniu do innych technologii, takich jak hydraulika czy elektryka.
Jakie zastosowania mają maszyny pneumatyczne w przemyśle
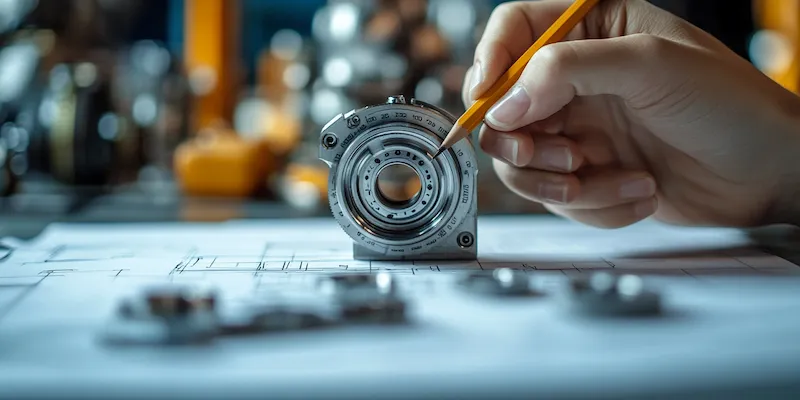
Maszyny pneumatyczne znajdują szerokie zastosowanie w różnych dziedzinach przemysłu dzięki swojej wszechstronności i efektywności. W przemyśle produkcyjnym często wykorzystuje się je do automatyzacji procesów montażowych oraz pakowania produktów. Siłowniki pneumatyczne są powszechnie stosowane do podnoszenia i przenoszenia ciężkich elementów, co znacząco zwiększa wydajność pracy oraz redukuje ryzyko urazów u pracowników. W branży motoryzacyjnej maszyny pneumatyczne są wykorzystywane do malowania pojazdów oraz aplikacji lakierów, ponieważ umożliwiają równomierne pokrycie powierzchni. Również w sektorze spożywczym maszyny te odgrywają ważną rolę, na przykład przy pakowaniu żywności czy transportowaniu produktów między różnymi etapami produkcji. Ponadto, systemy pneumatyczne znajdują zastosowanie w urządzeniach medycznych, takich jak aparaty do wentylacji czy urządzenia do diagnostyki obrazowej.
Jakie są nowoczesne technologie w budowie maszyn pneumatycznych
W ostatnich latach budowa maszyn pneumatycznych uległa znacznym zmianom dzięki postępom technologicznym oraz innowacjom inżynieryjnym. Nowoczesne technologie umożliwiają zwiększenie efektywności energetycznej systemów pneumatycznych oraz poprawę ich wydajności. Przykładem jest zastosowanie inteligentnych czujników i systemów monitorujących, które pozwalają na bieżąco śledzić parametry pracy maszyny oraz optymalizować jej działanie. Dzięki temu możliwe jest zminimalizowanie strat energii oraz zwiększenie precyzji operacji wykonywanych przez maszyny pneumatyczne. Kolejnym trendem jest rozwój materiałów kompozytowych oraz lekkich stopów metali, które pozwalają na budowę bardziej wytrzymałych i jednocześnie lżejszych komponentów maszyn. Warto również zwrócić uwagę na rosnącą popularność automatyzacji procesów produkcyjnych oraz integracji maszyn pneumatycznych z systemami robotyzacji. Takie podejście pozwala na jeszcze większą elastyczność produkcji oraz szybsze dostosowywanie się do zmieniających się potrzeb rynku.
Jakie są kluczowe aspekty bezpieczeństwa w maszynach pneumatycznych
Bezpieczeństwo w pracy z maszynami pneumatycznymi jest niezwykle istotnym zagadnieniem, które należy uwzględnić na każdym etapie ich eksploatacji. W pierwszej kolejności, kluczowym elementem jest odpowiednie szkolenie pracowników, którzy będą obsługiwać te maszyny. Powinni oni być dobrze zaznajomieni z zasadami działania systemów pneumatycznych oraz umieć rozpoznać potencjalne zagrożenia związane z ich użytkowaniem. Dodatkowo, istotne jest stosowanie odpowiednich środków ochrony osobistej, takich jak rękawice, gogle czy kaski, które mogą chronić pracowników przed ewentualnymi urazami. Kolejnym ważnym aspektem jest regularne przeprowadzanie przeglądów technicznych oraz konserwacji maszyn pneumatycznych. Dzięki temu można zidentyfikować i usunąć wszelkie usterki, które mogłyby prowadzić do awarii lub wypadków. Należy również zwrócić uwagę na właściwe oznakowanie stref niebezpiecznych oraz stosowanie osłon i zabezpieczeń mechanicznych, które mogą ograniczyć dostęp do ruchomych części maszyny.
Jakie są różnice między maszynami pneumatycznymi a hydraulicznymi
Maszyny pneumatyczne i hydrauliczne to dwa różne typy systemów mechanicznych, które mają swoje unikalne cechy i zastosowania. Podstawową różnicą między nimi jest medium robocze – maszyny pneumatyczne wykorzystują sprężone powietrze, podczas gdy maszyny hydrauliczne operują cieczą pod wysokim ciśnieniem. Ta różnica ma znaczący wpływ na sposób działania obu systemów. Maszyny pneumatyczne są zazwyczaj lżejsze i prostsze w budowie, co sprawia, że są bardziej mobilne i łatwiejsze do zainstalowania w różnych lokalizacjach. Z drugiej strony, maszyny hydrauliczne oferują większą siłę i precyzję działania, co czyni je idealnym rozwiązaniem w zastosowaniach wymagających dużych obciążeń lub skomplikowanych ruchów. Warto również zauważyć, że systemy pneumatyczne są bardziej odporne na działanie substancji chemicznych oraz zmiany temperatury, co czyni je bardziej uniwersalnymi w trudnych warunkach. Jednakże, ze względu na mniejszą efektywność energetyczną, maszyny hydrauliczne często znajdują zastosowanie tam, gdzie wymagana jest wysoka moc i precyzyjne sterowanie.
Jakie są najnowsze trendy w projektowaniu maszyn pneumatycznych
W ostatnich latach projektowanie maszyn pneumatycznych ewoluuje pod wpływem nowych technologii oraz rosnących oczekiwań rynku. Jednym z najważniejszych trendów jest dążenie do zwiększenia efektywności energetycznej systemów pneumatycznych. Inżynierowie poszukują innowacyjnych rozwiązań, które pozwolą na minimalizację strat energii oraz optymalizację procesów produkcyjnych. Przykładem może być zastosowanie inteligentnych systemów sterowania, które automatycznie dostosowują parametry pracy maszyny do aktualnych potrzeb produkcji. Kolejnym istotnym trendem jest rozwój modułowych konstrukcji maszyn pneumatycznych, które umożliwiają łatwe dostosowywanie ich do zmieniających się warunków pracy oraz specyfiki produkcji. Dzięki modułowości możliwe jest szybkie dodawanie lub usuwanie komponentów bez konieczności przeprowadzania skomplikowanych modyfikacji całego systemu. Również rosnące zainteresowanie automatyką przemysłową wpływa na projektowanie maszyn pneumatycznych – integracja z robotami oraz systemami zarządzania produkcją staje się standardem w nowoczesnych zakładach przemysłowych.
Jakie są koszty eksploatacji maszyn pneumatycznych
Koszty eksploatacji maszyn pneumatycznych mogą być zróżnicowane i zależą od wielu czynników, takich jak rodzaj zastosowanej technologii, intensywność użytkowania czy potrzeby konserwacyjne. W pierwszej kolejności należy uwzględnić koszty energii związane z działaniem sprężarek powietrza. Sprężone powietrze jest jednym z najdroższych mediów energetycznych, dlatego optymalizacja jego zużycia ma kluczowe znaczenie dla obniżenia kosztów eksploatacyjnych. Dodatkowo warto zwrócić uwagę na koszty związane z konserwacją i serwisowaniem maszyn – regularne przeglądy techniczne oraz wymiana zużytych komponentów mogą generować znaczne wydatki w dłuższym okresie czasu. Koszty zakupu części zamiennych również powinny być brane pod uwagę przy planowaniu budżetu eksploatacyjnego. Należy także pamiętać o kosztach szkolenia pracowników obsługujących maszyny pneumatyczne – inwestycja w odpowiednie przygotowanie personelu może przynieść długofalowe korzyści w postaci zwiększonej wydajności oraz mniejszej liczby awarii.
Jakie są przyszłościowe kierunki rozwoju technologii pneumatycznej
Przyszłość technologii pneumatycznej zapowiada się obiecująco dzięki ciągłemu rozwojowi innowacyjnych rozwiązań oraz rosnącemu zainteresowaniu automatyzacją procesów przemysłowych. Jednym z kluczowych kierunków rozwoju będzie integracja systemów pneumatycznych z nowoczesnymi technologiami informacyjnymi i komunikacyjnymi. Dzięki temu możliwe będzie tworzenie inteligentnych fabryk, gdzie maszyny będą mogły autonomicznie dostosowywać swoje parametry pracy do aktualnych potrzeb produkcji oraz wymagań jakościowych. Również rozwój Internetu rzeczy (IoT) wpłynie na sposób monitorowania i zarządzania systemami pneumatycznymi – dzięki zastosowaniu czujników i analizy danych możliwe będzie przewidywanie awarii oraz optymalizacja procesów produkcyjnych w czasie rzeczywistym. Kolejnym istotnym trendem będzie dążenie do zwiększenia efektywności energetycznej poprzez rozwój nowych materiałów oraz technologii sprężania powietrza. W miarę jak coraz więcej firm stawia na zrównoważony rozwój i ekologiczne rozwiązania, technologie pneumatyczne będą musiały dostosować się do tych wymagań poprzez redukcję emisji CO2 oraz zmniejszenie zużycia energii.